3D-Printed Air Purification Skin
Parametric Add-on Solution for Architecture and More

Project name:
Air Purification Skin
Software:
Rhino[Grasshopper], Vray
Material:
ABS, PLA, TPU
Presentation:
Link︎︎︎
Date:
2022 - 2023
3D printing techniques have created new opportunities for humans in many aspects, such as fashion, manufacturing, space projects, and housing. The ability to produce high-quality intricate shapes could be the key to addressing some long-standing, inevitable problems caused by traditional building constructions. Since fall 2022, I have been working with 3D printing techniques to design an innovative add-on cladding system capable of filtering air. The study focuses on the Textile Center Building in downtown Los Angeles as its first applied prototype.
Air Purification Skin
Software:
Rhino[Grasshopper], Vray
Material:
ABS, PLA, TPU
Presentation:
Link︎︎︎
Date:
2022 - 2023
3D printing techniques have created new opportunities for humans in many aspects, such as fashion, manufacturing, space projects, and housing. The ability to produce high-quality intricate shapes could be the key to addressing some long-standing, inevitable problems caused by traditional building constructions. Since fall 2022, I have been working with 3D printing techniques to design an innovative add-on cladding system capable of filtering air. The study focuses on the Textile Center Building in downtown Los Angeles as its first applied prototype.
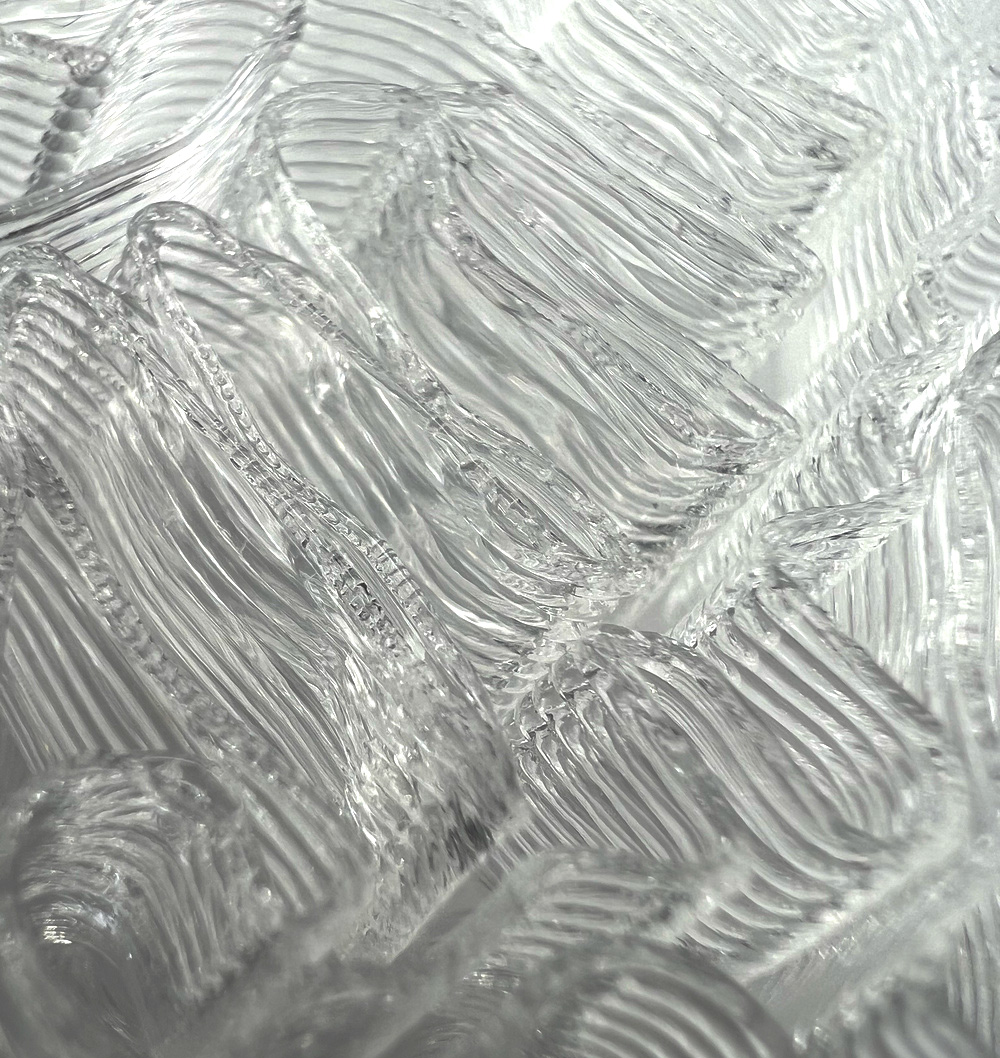
This study encompasses four stages of development: firstly, investigating the water-filtering capacity and growth structure of brain coral through biological research. Secondly, creating parametric patterning prototypes. Thirdly, experimenting with various 3D printing methods and filaments. Lastly, implementing the final design in a real architectural context.



The newly designed air purification skin is a 3D-printed, easy-to-install, and sustainable add-on structure for building facades. The intricate patterns are specifically designed for different parts of the facade. The curvature extrusion serves as a dust barrier for the building by trapping the particles and screening them out. The panels are 3D printed flat off-site with translucent ABS filament that has a wide range of temperature endurance from -4 F to 176 F. The translucency of the cladding allows visions through both sides and provides a unique aesthetic value to the new building's appearance at the same time.

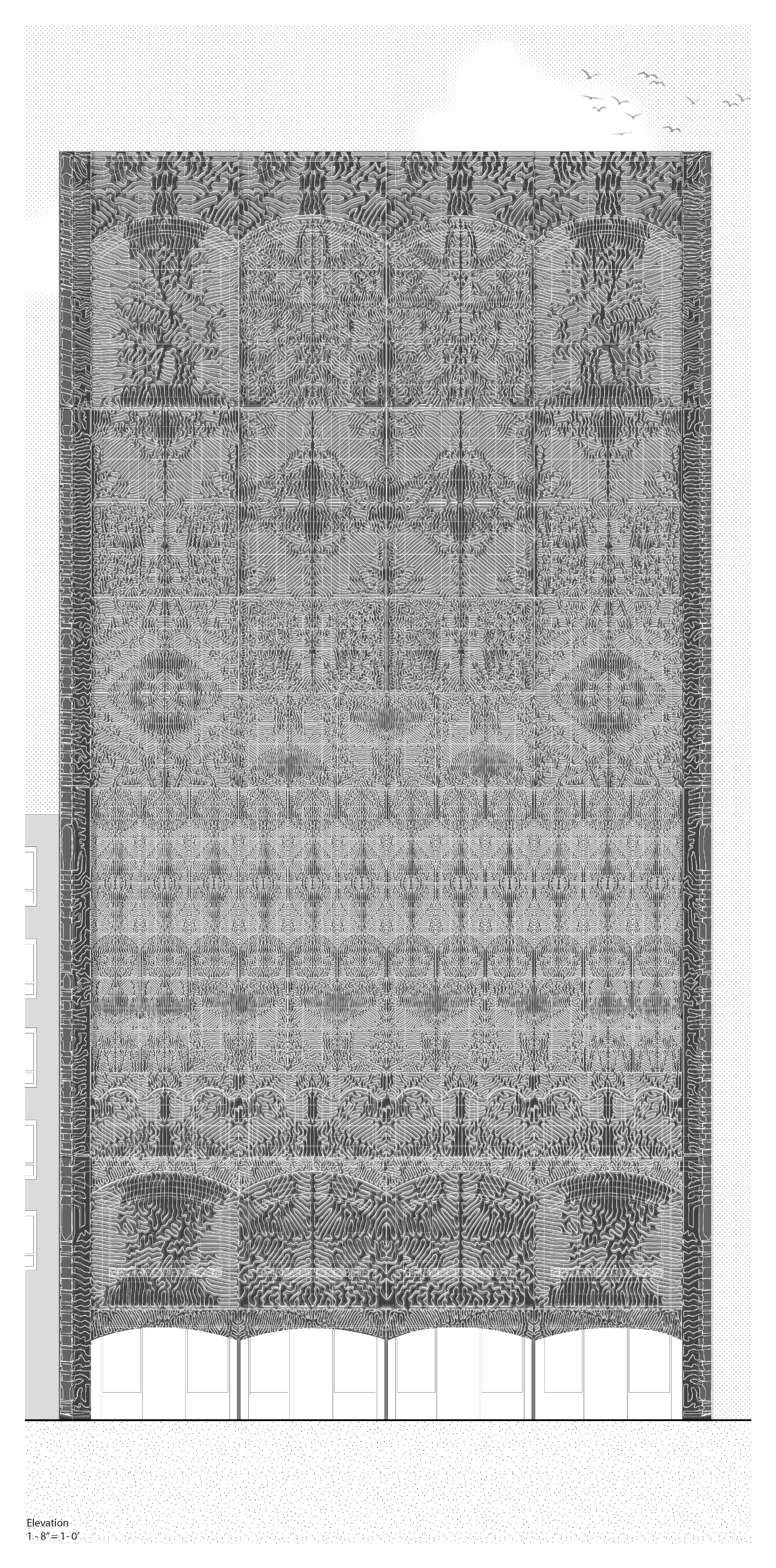

The generation process offers two distinct options: starting from a central point and expanding towards the edges, or commencing from the edges of a polygon within a defined boundary and expanding both inward and outward. Opting for the former approach would result in the curve gradually growing along the surface edge, ultimately emphasizing the presence of the surface outline. This particular technique is employed to reinforce the historical ornaments showcased on the textile center building. On the other hand, choosing the latter generation method would yield an intricately organic and undulating pattern along the surface edges. With its increased surface area, this pattern excels at filtering and purifying the incoming air, effectively capturing pollutants. Both techniques are able to generate patterns with clear branching numbers and directions. The branching system is embedded in the pattern as both the figure and void. The numbers of branching divisions used in this prototype are 3,4,5,6. The aggregation of multiple branching patterns provides flexible arrangement and dynamic aesthetics.
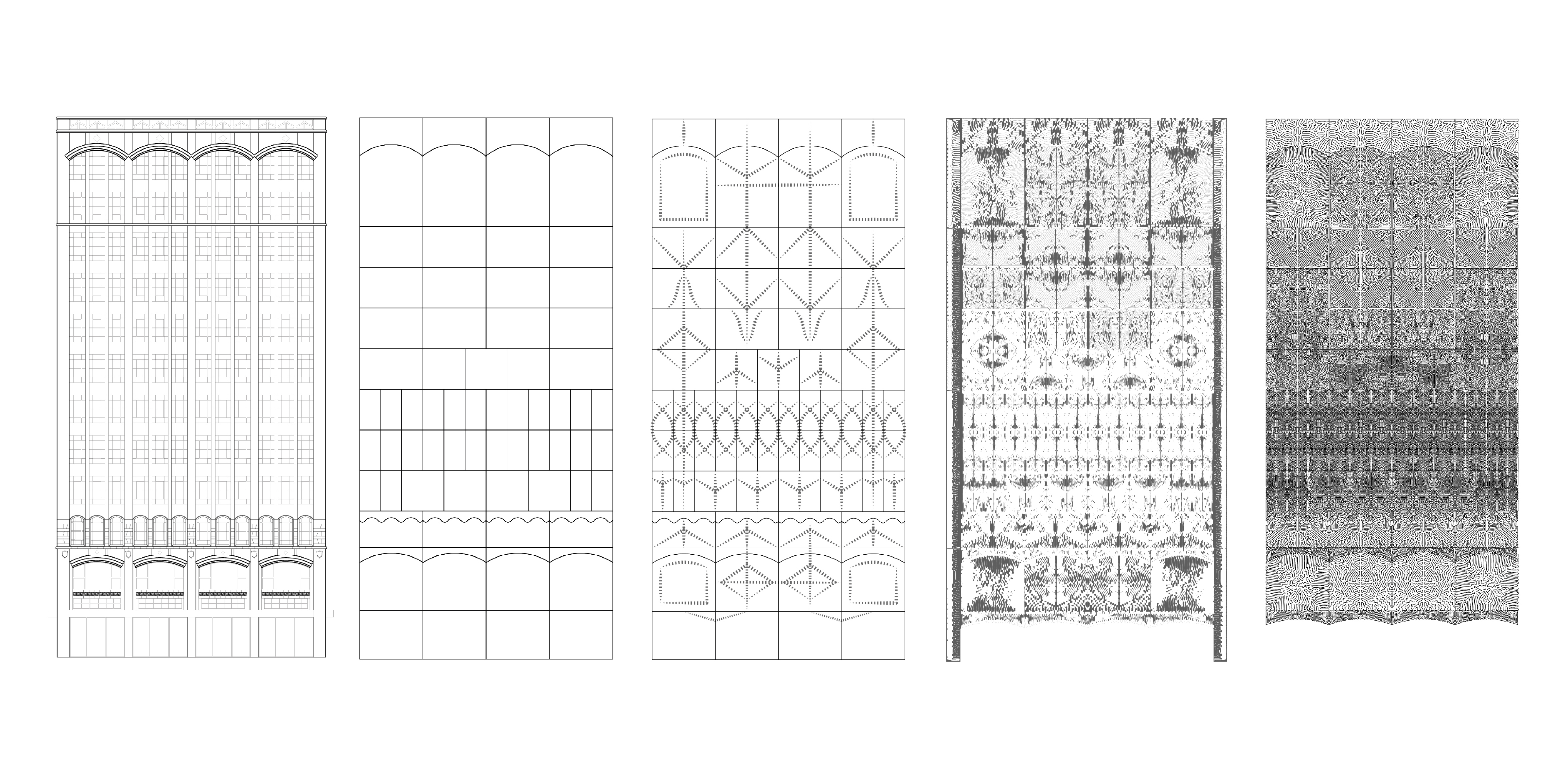
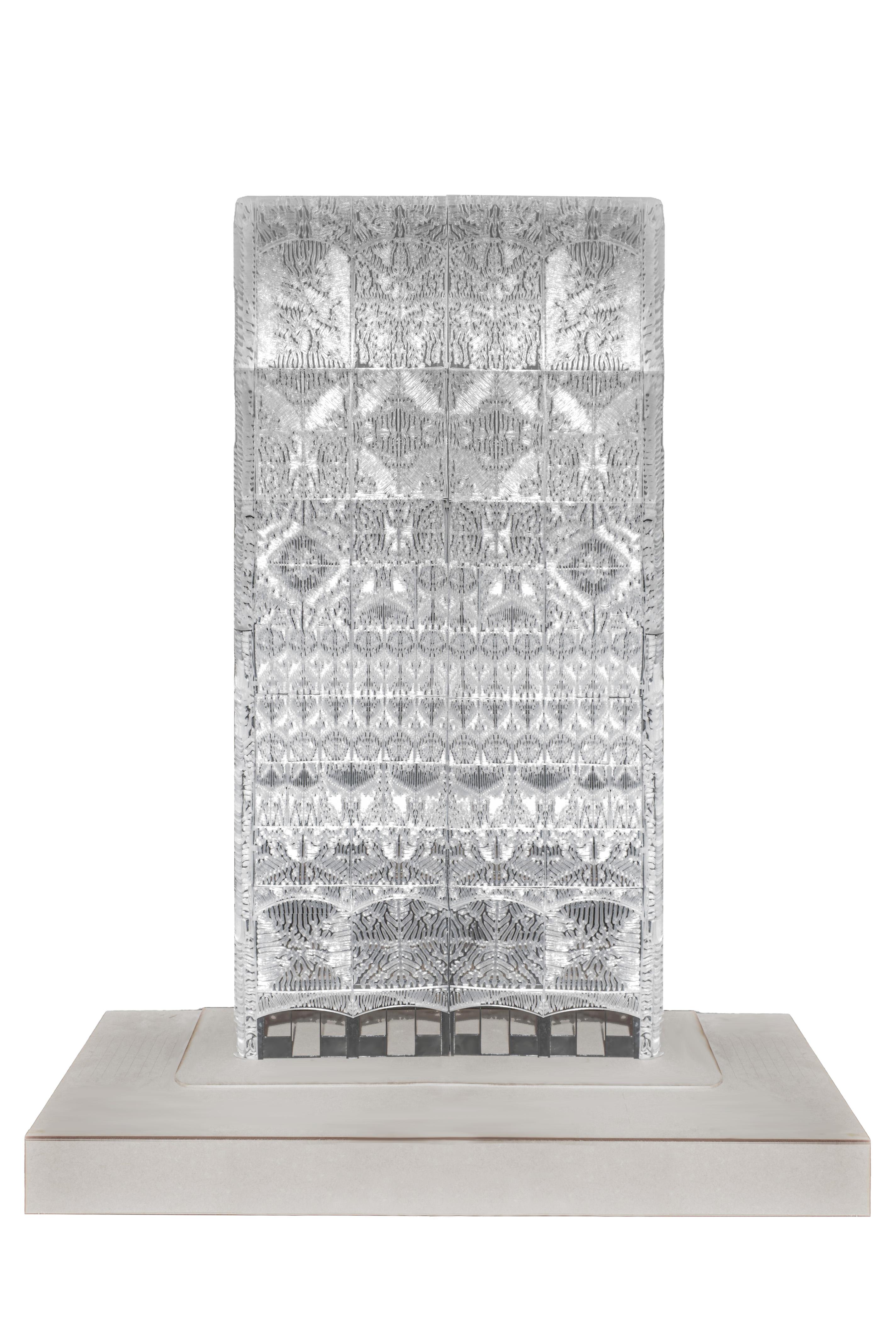
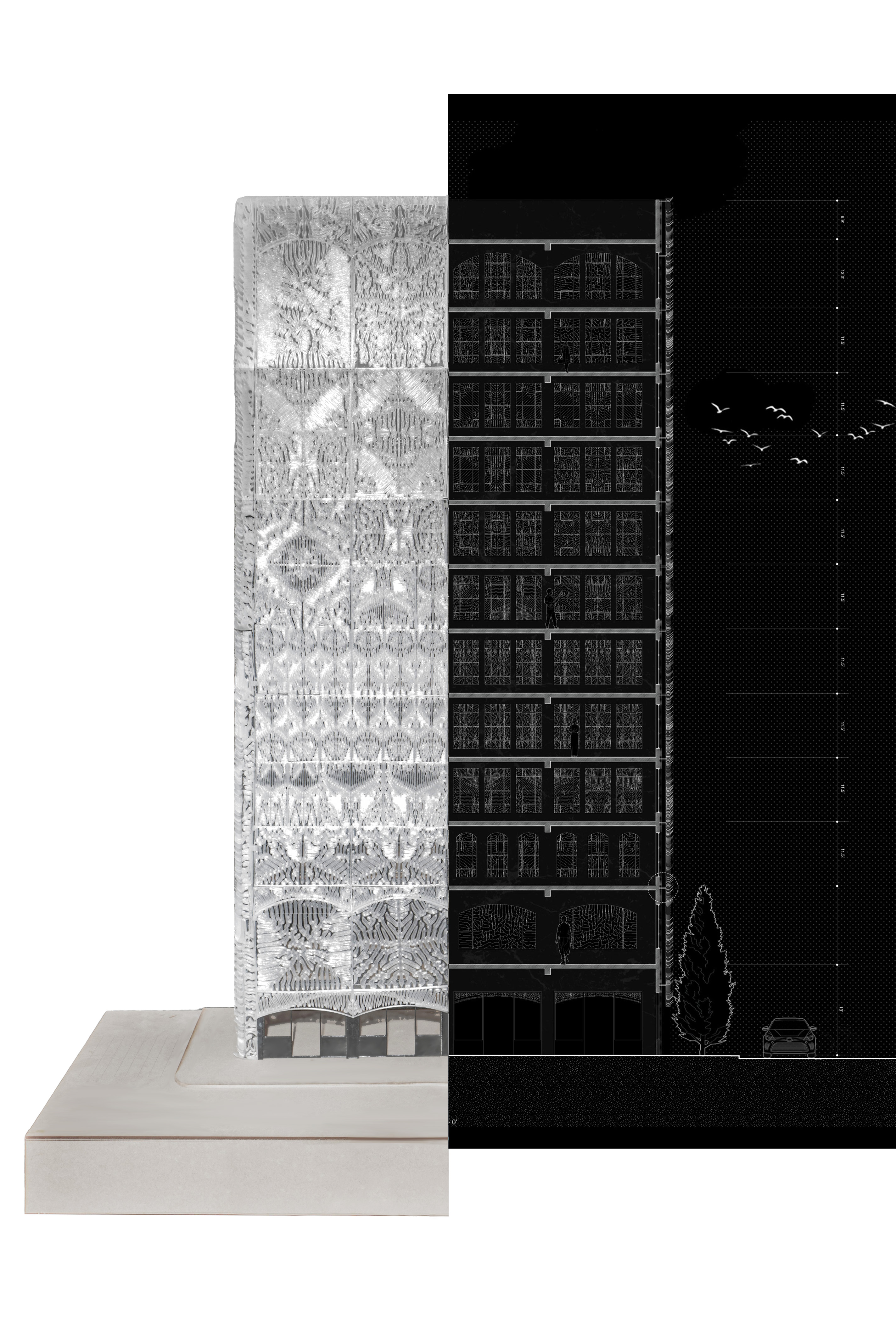
This gradient density effect smooths the articulation between panels with different densities. Additionally, it allows one panel to perform at different levels of privacy which is necessary when one single panel covers various rooms with different programs in the building. For instance, the bottom levels of the building are occupied with commercial space and short-term visitors, which need less privacy, while the residential levels inthe middle require comparably more. The changing density on the cladding is the reflection of social activities and programs.
Zero-Support 3D-prints with PLA and TPU

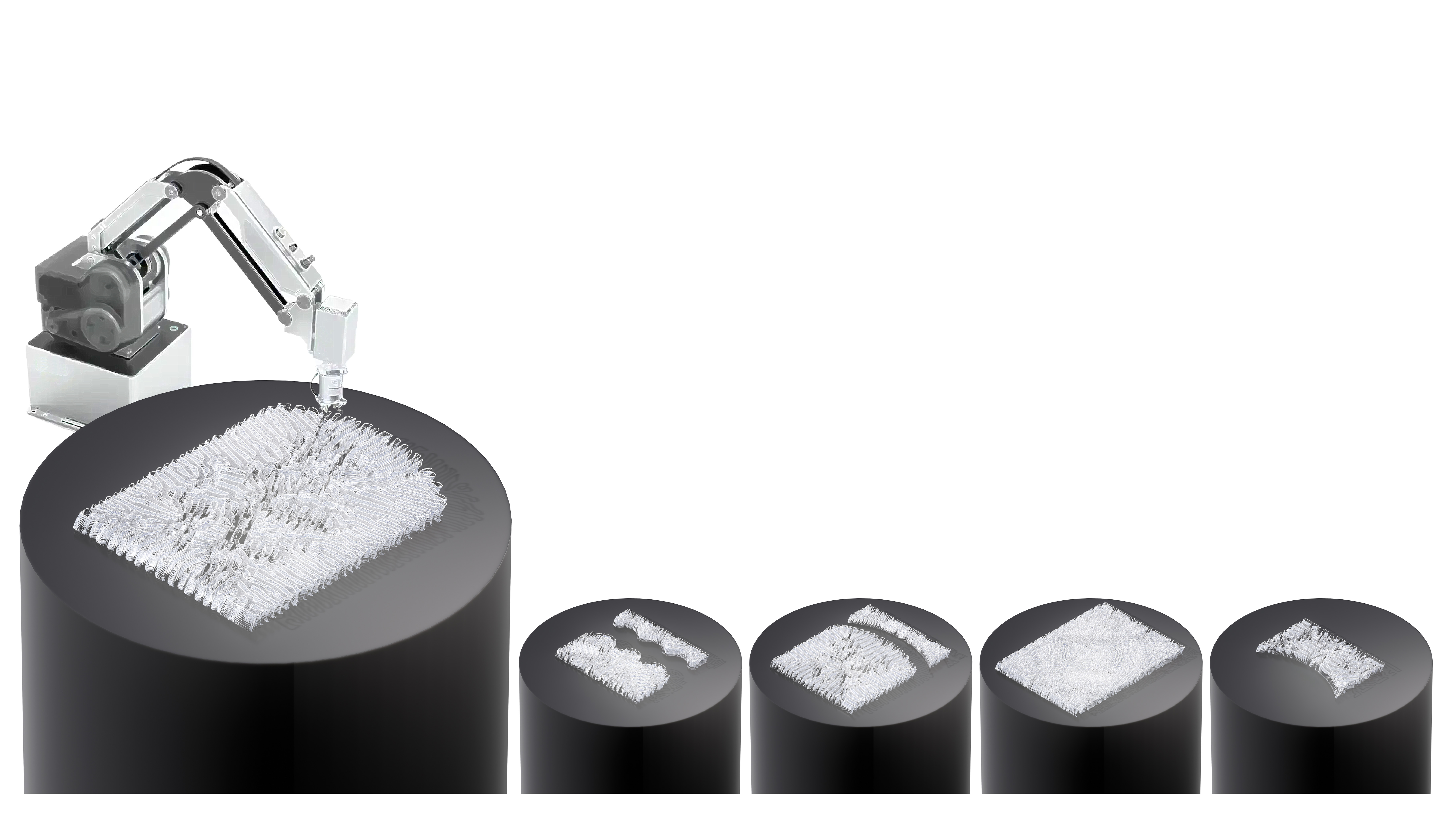
The installation of the air purification skin requires an aluminum frame structure to contain each individual 3D-printed structure and be mounted onto the existing building facade. Each pattern
will be 3D-printed off-site with a depth of 15 inches extruded along a sheared curve from the ground. The sheared angle of the building side is set at 66 degrees, while the exterior side is
angled at 44 degrees. This design allows for efficient distribution and navigation of air through the air purification screen, effectively trapping pollutants within the sunken area. Moreover, the
translucent angled screen serves a dual purpose by providing optimal shading and ensuring a certain level of privacy for the residents within the building. For the normal 3D-printing method,
66 degrees is a challenging angle to handle, but the air purification skin only requires contour
printing. That is to say, the printer only goes along the closed pattern, no infill is needed. Each layer is slightly offset from the bottom layer, which allows a sharp angle to be printed vertically
without any support. Plus, less filament used contributes to more effective production. Once the 3D-printed part is completed, it will be clipped into an aluminum frame and shipped to the site.
The panels will be articulated together piece by piece. Several bricks from the old cladding will be replaced by concrete in order to fix the aluminum tube.
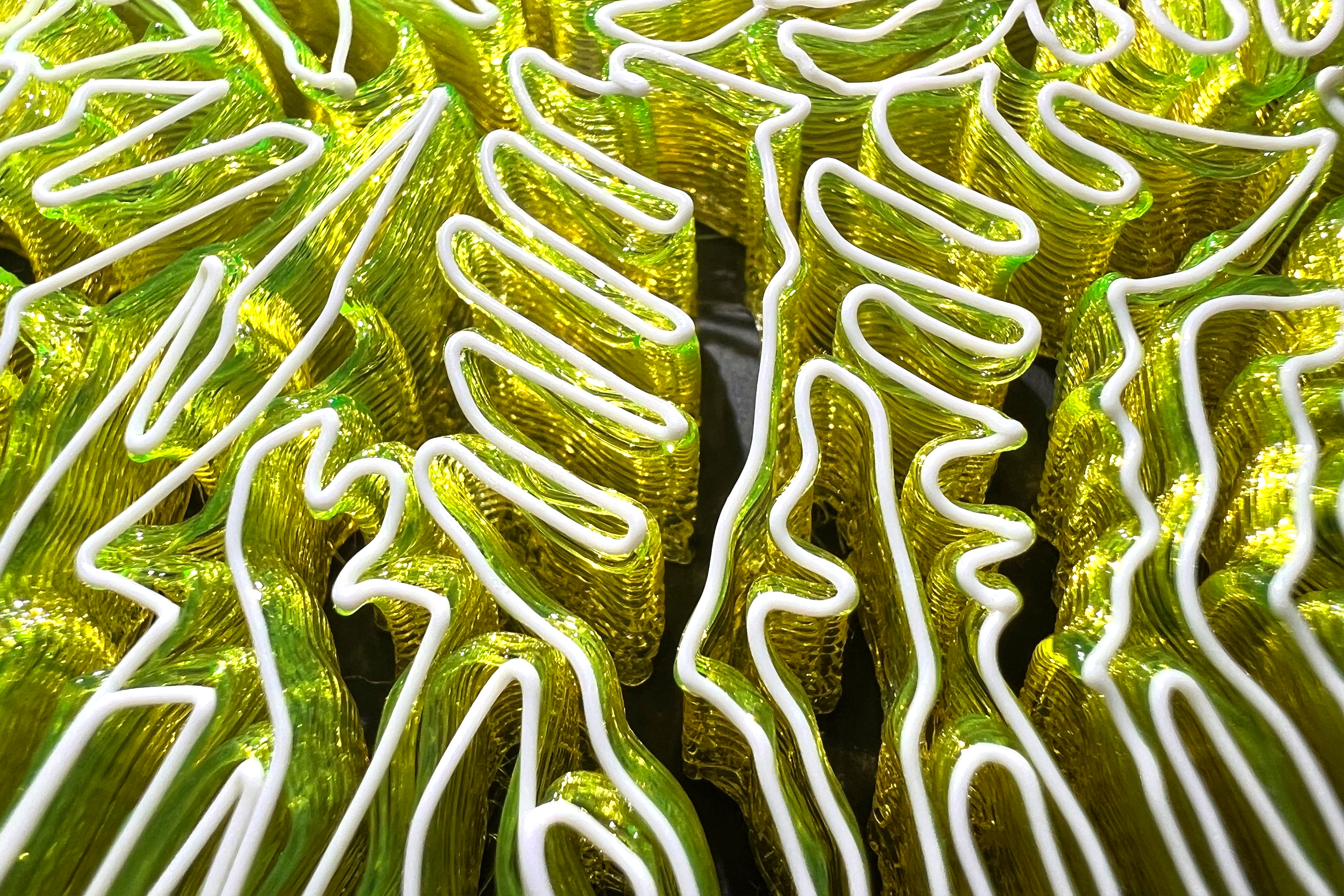


@ Rui Qiu